ELANTAS is a firm believer that eMobility in connection with renewable energy is the key for future sustainable mobility and reduction of global emissions. To support the growth of eMobility globally we support this market with innovative products which help to operate electric vehicles safely and enable innovative, cost efficient solutions through our products. As a market leader for electrical insulating and protection materials ELANTAS has over 100 years of experience in the industry.
Wide range of protection and insulation materials for electric vehicles
The ELANTAS product portfolio offers a broad range of protection and electrical insulation materials that can be found in the motor, powertrain, battery and other electronic components of a vehicle.
Different chemistries are available to provide the product with the best properties for the application. ELANTAS also offers customized solutions for specific application needs which are developed together with our customers.
Global Presence for a Global Industry
Our global team of R&D experts and technical managers are working closely with customer design engineers and technical staff to solve their issues, and are supported by the local ELANTAS application labs in the regions.
As an experienced supplier to the automotive industry ELANTAS understands the requirements and expectations throughout the entire automotive value chain and is working according to given standards (IATF 16949). Local supply options from our manufacturing sites in the regions results in short lead time.
Electric motors for eMobility applications are used in more and more road and off-road vehicles, ships and even aircraft. They can be the sole engine (e.g. in electric vehicles (EV)) or they can be combined with a combustion engine (e.g. in hybrid vehicles (HEV) or in Plug-in hybrid vehicles (PHEV)). For example, hybrids are connected in series with a gearbox system or operate in parallel such as an in-wheel eMotor.
Rising market demand for thermal efficiency and effective insulation in eMotors
Each motor design places its own special requirements on the insulation system. Space in vehicles is limited, so power density is paramount. Efficient thermal management and a highly effective insulation system are important in achieving this design goal.
The fast-growing electromobility market encourages rapid innovation, where production speed and efficiency being very important drivers for business success. The use of hair-pin coil motors is becoming standard in eMobility applications, because of their high copper fill factor and levels of efficiency.
ELANTAS solutions enable longer lifetimes for electric motors
With the development towards 400 or 800V power systems high-performance powertrains, partial discharge resistance of the insulation system is a key parameter in achieving long electric motor lifetimes. In accordance with these new requirements ELANTAS offers superior insulation systems consisting of wire enamels, flexible insulation materials as well as impregnating and potting resins.
Supported by global R&D centers and productions sites, ELANTAS offers tailored solutions for your insulation system depending on motor design, operation conditions and environmental requirements.
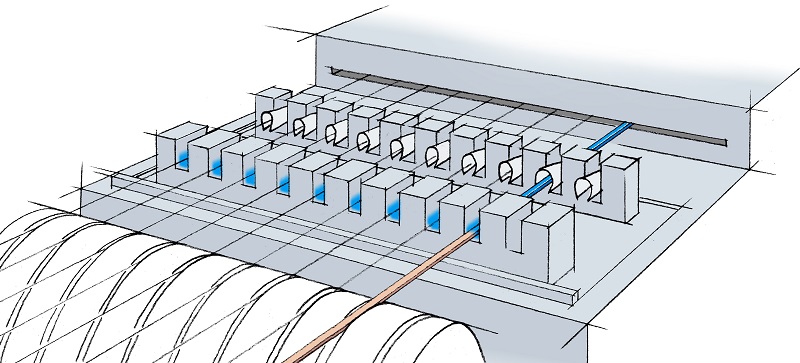
Wire Enamels
Wire Enamels
Wire enamels are special coatings applied to copper and aluminum wires to ensure electrical insulation of the magnet wires.
ELANTAS develops and manufactures wire enamels based on different chemistries according to individual requirements. With our global presence, ELANTAS guarantees reliable supply and consistently high quality in all regions.
High demands on thermal and mechanical stability of the wire enamels
Apart from the basic electrical insulation, wire enamels that are applied to traction motors for electromobility must possess:
- High thermal and mechanical stability and chemical durability.
- In motors for electric vehicles where the system of utilizes 400/800V, the enamel on the magnet wire must also provide resistance to high partial discharge characteristics.
ELANTAS new developments on Corona resistance Polyamide-imide and high temperature stable Polyimide facilitate future developments in eMobility.
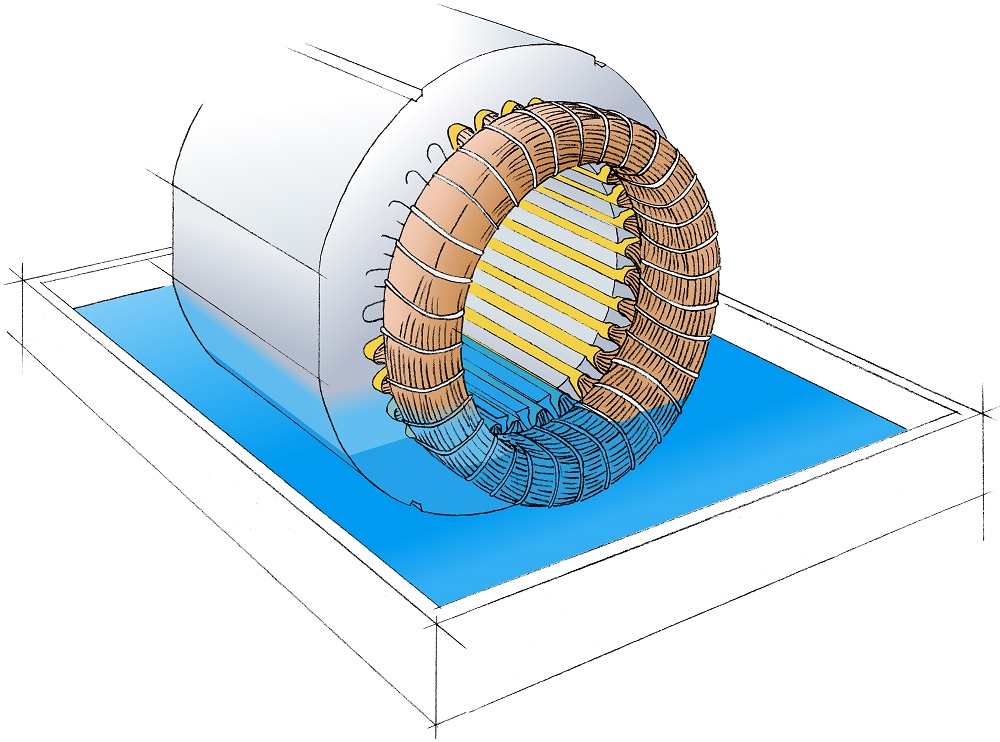
Impregnating Materials
Impregnating Materials
Impregnating materials provide protection against:
- mechanical,
- thermal,
- environmental
- electrical stresses
to extend motor life as electrical motors are subject to many stresses during their lifetime which can cause the insulation system to fail.
With our multi chemistry approach ELANTAS offers products for different operating conditions of your motor.
In addition, the selection of the right impregnating material is subject to
- the motor design and
- processing technique to ensure void free filling.
ELANTAS product portfolio covers all common processing methods for electromobility applications such as
- Trickle
- Dipping
- Dip-rolling
- Hot dipping with/without UV curing
- Vacuum Pressure Impregnation (VPI)
Globally, our technical experts with application labs can provide processing support to simulate industrial conditions and are available to advise you regarding both the selection of the material and its use in the production.
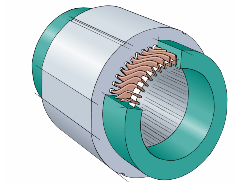
Casting Materials
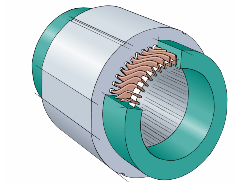
Casting Materials
To increase the lifetime of a motor the stator can be protected with casting materials against
- electrical,
- mechanical,
- thermal and
- environmental stresses.
Depending on motor design and operating conditions the full stator (or just the winding head) can be casted. Insulation by casting materials results in improved thermal conductivity and noise reduction but lead to an increase motor weight vs. impregnation technology.
ELANTAS offers casting materials which may be adjusted according to the processing conditions and motor design. These are characterized by:
- good thermal conductivity,
- low shrinkage and
- excellent chemical resistance
Our team of technical sales managers and application technicians are available to select and test the appropriate material for your needs.
Wire Enamels
Wire enamels are special coatings applied to copper and aluminum wires to ensure electrical insulation of the magnet wires.
ELANTAS develops and manufactures wire enamels based on different chemistries according to individual requirements. With our global presence, ELANTAS guarantees reliable supply and consistently high quality in all regions.
High demands on thermal and mechanical stability of the wire enamels
Apart from the basic electrical insulation, wire enamels that are applied to traction motors for electromobility must possess:
- High thermal and mechanical stability and chemical durability.
- In motors for electric vehicles where the system of utilizes 400/800V, the enamel on the magnet wire must also provide resistance to high partial discharge characteristics.
ELANTAS new developments on Corona resistance Polyamide-imide and high temperature stable Polyimide facilitate future developments in eMobility.
Impregnating Materials
Impregnating materials provide protection against:
- mechanical,
- thermal,
- environmental
- electrical stresses
to extend motor life as electrical motors are subject to many stresses during their lifetime which can cause the insulation system to fail.
With our multi chemistry approach ELANTAS offers products for different operating conditions of your motor.
In addition, the selection of the right impregnating material is subject to
- the motor design and
- processing technique to ensure void free filling.
ELANTAS product portfolio covers all common processing methods for electromobility applications such as
- Trickle
- Dipping
- Dip-rolling
- Hot dipping with/without UV curing
- Vacuum Pressure Impregnation (VPI)
Globally, our technical experts with application labs can provide processing support to simulate industrial conditions and are available to advise you regarding both the selection of the material and its use in the production.
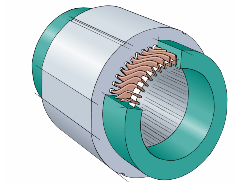
Casting Materials
To increase the lifetime of a motor the stator can be protected with casting materials against
- electrical,
- mechanical,
- thermal and
- environmental stresses.
Depending on motor design and operating conditions the full stator (or just the winding head) can be casted. Insulation by casting materials results in improved thermal conductivity and noise reduction but lead to an increase motor weight vs. impregnation technology.
ELANTAS offers casting materials which may be adjusted according to the processing conditions and motor design. These are characterized by:
- good thermal conductivity,
- low shrinkage and
- excellent chemical resistance
Our team of technical sales managers and application technicians are available to select and test the appropriate material for your needs.
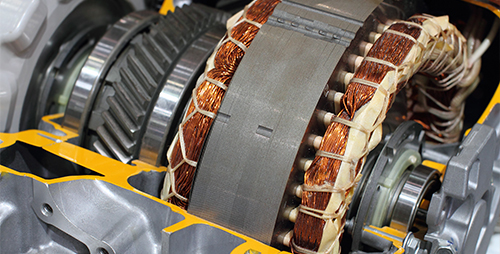
Stators are the stationary part of an electric motor and provide a rotating magnetic field that drives the rotating armature. The core of the stator is built up of high-grade alloy steel laminations, which is wound with round or flat wire conductors into slots. Once the winding of a stator has been completed, the final stage of manufacture will be to bond the winding by using an impregnating or encapsulating process.
Other benefits that can be derived from the Impregnation or Encapsulation process would be void filling in the slot or improved thermal flow as well as increases chemical resistance, environmental protection and mechanical wear and damage. In general, the process ensures:
- Electrical insulation
- Chemical protection
- Mechanical protection
Processing Methods
The application method to apply the impregnation or the encapsulation resins are quite different. However, the process should ensure the wound coils in the slots are fully saturated and void free.
Impregnation ProcessThere are several processes by which the impregnation resins can be applied, the determination as to which method to use depends on the dimensions of the stator and the daily product quantity. A summary of various impregnation processes is listed in the table below:
* Vacuum Pressure Impregnation
Encapsulation Process
Many variations on a standard encapsulation process are available. In principle the stator is placed into a mold, then resin is poured over the winding head. After the resin has entered the wound coils in the slots following a gelation and curing process. The cure may be performed at ambient temperature or at elevated temperature in an oven. Applying vacuum during the process will result in an excellent, void free encapsulation.
Advantage/disadvantage of encapsulating vs. impregnation
Requirements for eMobility application
Electrical insulation materials for eMobility motors face conflicting requirements. The eMobility motor is required to deliver high torque for brief periods and low torque for long periods. It will be subjected to a variety of environmental conditions from both high and low ambient temperature conditions, be resistant to oils, water, and salt from winter streets. Long-term reliability is an absolute, the electrical insulation must be tough enough to withstand high temperatures and chemicals, but also possess some degree of flexibility to manage temperature shocks and mechanical stress applied to the motor windings due the torque the motor develops.
ELANTAS offers an extensive portfolio of high-performance materials for stator impregnating or encapsulating which meets the main requirements as:
- Very good chemical resistance
- Temperature Shock Resistance
- VOC-free product range
- Product portfolio for all processing methods
- High thermal conductive materials
- Partial discharge resistance
ELANTAS's globally available product range, ELAN-drive widely used in eMobility application:
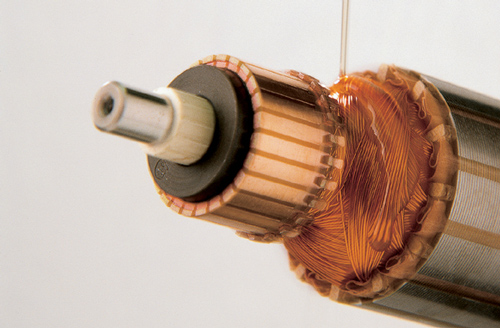
Today, rotors used for e-motors in electric cars are designed as Wound Rotors or Permanent Magnet Rotor (PM) in particular when higher power density is required. Depending on the rotor type and selected processing technology different materials are essential.
ELANTAS offers for all type of rotors and processing technologies the best material to stabilize the rotor against extreme centrifugal forces.
ELANTAS products has proven superior properties in EV motors as:
- Bonding at high rotation speed
- Thermal shock stability
- Support thermal management
- Chemical resistance to aggressive oils and cooling fluids
The below table gives an overview on most common applied processing technologies, products and main characteristics in the manufacturing of wound rotors for e-motors:
Permanent Magnet Motors
Instead of coils, permanent magnet motors use strong magnets for the rotor element to generate the magnetic field. Collectively, these magnets need to be tightly fixed to the rotor steel package or the rotor housing. Motor developers have come up with various designs of magnet arrangements. Some magnets are pushed into pockets in the steel package of the rotor and are fixed with low viscous adhesive that fills the pocket; other magnets are fixed to the outside of the rotor which obviously is different as to the required adhesive strength and viscosity during application. Mostly, the maximum operation temperature of Magnets shall not exceed 80°C. For special high-end use in automotive the rotors are tested until 150°C.
ELANTAS products offered for magnet fixation
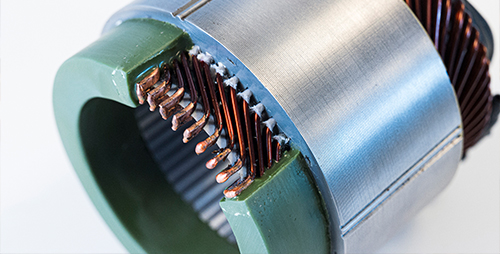
Electric motors for eMobility applications require higher power and torque at limited constructed space and weight in a car. This can be achieved by increasing the copper fill factor in the slots of the stator. Hence, flat wires are applied in the latest development of motors, especially for premium cars.
Hair-Pin Technology
While conventional round wires are wound into the slots; flat wires must be inserted into the stator by the i-Pin or Hair Pin technique and thereof require welding on one or both sides of the copper pins connections following by insulation of the welded pins. Various technologies can be applied for this purpose:
- Epoxy Powder coating,
- Potting
- Impregnation
ELANTAS hair-pin protection solutions save time and budget.
While Epoxy powder coating requires an additional process step, ELANTAS offers insulation materials which can be applied in one process step and with similar process equipment used today. Applying ELANTAS solutions further process benefits as reduced investment and faster process time can generated.
ELANTAS has screened various electrical insulating materials for Hair Pin Protection and developed materials. During the extensive study (LINK) of materials in combination with the application technique ELANTAS developed materials with:
- excellent edge coverage
- excellent thermal shock resistance
- oil compatibility
- application by a conventional processing technique
As further requirement based on the motor design and operation condition needs to be considered, ELTANTAS offers our technical knowledge for individual technical consulting during the design, test and production phase.
The table below shows the most global applied ELAN-drive materials for Hair Pin Protection:
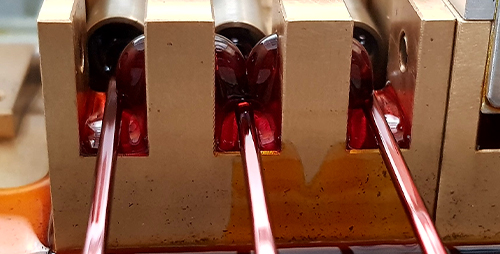
To create an electromagnetic field in an electric motor, a conductive coil where each conductor of the coils has an electrical insulation wire is required. For low and medium voltage machines, the electrical insulation otherwise known as primary insulation is created by laying down, in multiple passes, and enamel. The wire manufactured by this process is known as magnet wire. It is a unique product as the magnet wire, which comes in round or rectangular (flat) shaped wire and offers the following features:
- High dielectric properties
- High temperature durability
- Chemical resistance
- Excellent mechanical properties
Processing Methods
Motor coils are generally produced by high-speed winding or insertion machines. It is a requirements of motor manufacturers to produce electric motors as quickly and efficiently as possible to minimize costs. Magnet wire must withstand the forces applied to it to ensure the coils are tightly wound and compact, the magnet wire is pulled or threaded into the slots which exerts extreme force on the magnet wire and the primary coating. Finally, there may be a forming process to the wound coils which applies mechanical force so the magnet wire to form the required shape.
Requirements for eMobility application
For the eMobility motor application, the magnet wires must exhibit excellent thermal, electrical and mechanical properties. The shape of the magnet wire will be either round or rectangular, this will depend on the motor design. With increasing demands on high-voltage, high-output and large capacity motors, rectangle or flat wires with a higher space factor are more and more used for eMobility application to increase motor performance.
Round wire will need to be withstand high speed winding. The motors winding could also be subject to partial discharge. ELANTAS provides corona resistant protection such and special partial discharge resistant coatings. As the winding could be subject to high temperatures, coatings such as Polyamideimde and Polyimide are also available. ELANTAS offers both and even in combination with corona resistance properties.
For rectangular or flat wire ELANTAS has developed unique products covering variety of properties such as:
- High conformity of coating (edge covering)
- Layer thickness up to 150 µm
- Corona resistance
- High flexibility
- Good adhesion to conductor and secondary insulation
ELANTAS offers an extensive portfolio of high-performance enamels for magnet wire to meet the conflicting requirements. With ELANTAS excellent primers and self-lubricated enamels, wire structures can be extended further, and the performance can be improved to even higher level.
ELANTAS’s globally available product range ELAN-drive widely used in eMobility application:
*To achieve the best properties of a final magnet wire a combination of wire enamels is applied. Covering polyester or polyamide enamels with polyamide-imide leads to outstanding adhesion, dielectric and thermal properties. The resulting thermal index of such a combination will exceed 220°C (EIC and ASTM).
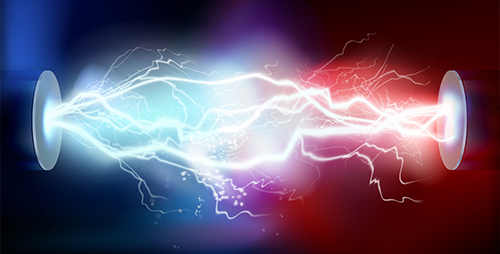
Recently, partial discharge has become a concern in lower voltage motors, especially for eMobility applications. These motors operate by variable speed drives (VSD). These drives control the motor speed using high frequency square waves as opposed to conventional sinusoidal waves. The frequencies incorporated are often up to 20 kHz, as compared to the conventional 50 or 60 Hz. VSD’s sometimes called ‘inverters’ offer great advantages such as high efficiency and fast accurate speed control.
Inverters are associated with problems such as voltage overshoots and reflected waves:
- Voltage overshoots vary in intensity but are often characterized by fast rise times.
- Reflected waves are a result of mismatched impedance.
The reflected wave becomes additive with another incoming wave resulting in a waveform that is twice the intended voltage. Since these waves are fast rise time, there is insufficient time for the energy to be dispersed among the windings of the motor. This creates high turn to turn potential between adjacent strands of magnet wire. These increased voltages are high enough to create partial discharge in the windings within the motor.
Partial discharge (PD) is defined as an ‘electrical discharge that does not completely bridge the space between two conducting electrodes.’ Areas with voids, cracks or imperfections is location where the partial discharge occurs.
Partial discharge occurs in void spaces in insulation and results in the damaging of the insulation system.
Protection by Encapsulation
ELANTAS offers a full package of insulation materials to improve lifetime and endurance under the influence of high voltage surges or partial discharge.
One solution to partial discharge is to remove the air where it occurs. Full encapsulation or potting of a motor with ELAN-tron® MC 62/W363 or ELAN-tron® MC 622/W363 is a great way to implements this solution.
Protection with Co-Shield® System
However, when full encapsulation is not being used, the best performance, is to utilize the Co-SHIELD® system. It provides superior resistance to partial discharge through the combination of wire enamels such as those described above impregnation resin such as the CORONA-Protect resins and ELAN-Film as flexible insulation material.
ELANTAS has developed magnet wire enamels which have demonstrated under pulse endurance testing longer life. The enamels provided by ELANTAS are the Corona Clear product and Allotherm CR along with the Tongmid CR products.
For an impregnation resin, the Corona Protect® 82-80A3 has shown that this has provided the longer life for EV motors particularly commercial electric vehicle applications.
Battery systems of electric cars are of high relevance for the success of electromobility. Market price of an electric vehicle, performance while driving and charging, longevity and maintaining the range, safety are just a few factors essentially determined by the battery.
ELANTAS products assure battery longevity
ELANTAS products protect cells and modules, and all electrical and electronic components within the pack to ensure safe and long-lasting operation, even under demanding driving conditions and charging cycles in all climate zones. ELANTAS battery solutions provide:
- electrical insulation
- thermal management
- adhesion and sealing functions
Battery packs, due to their complexity and size, contribute significantly to the cost of an electric car. Although prices have been cut significantly over the last decade the share can reach about a fifth of the new cars value.
At the same time, performance and longevity have been improved by selecting better active cell materials and also by employing specialty chemistry. Especially inthe assembly process of the cells to modules and packs specialty coatings and protection materials are now successfully applied.
High-performance products for energy storage
Innovation compete nce around the battery cell: ALTANA bundles its competencies in the battery sector. While BYK positively influences and optimizes the manufacturing process and performance of battery cells with a variety of high-quality additives, ELANTAS improves a wide range of applications outside the battery cell with TIM materials and gap fillers.
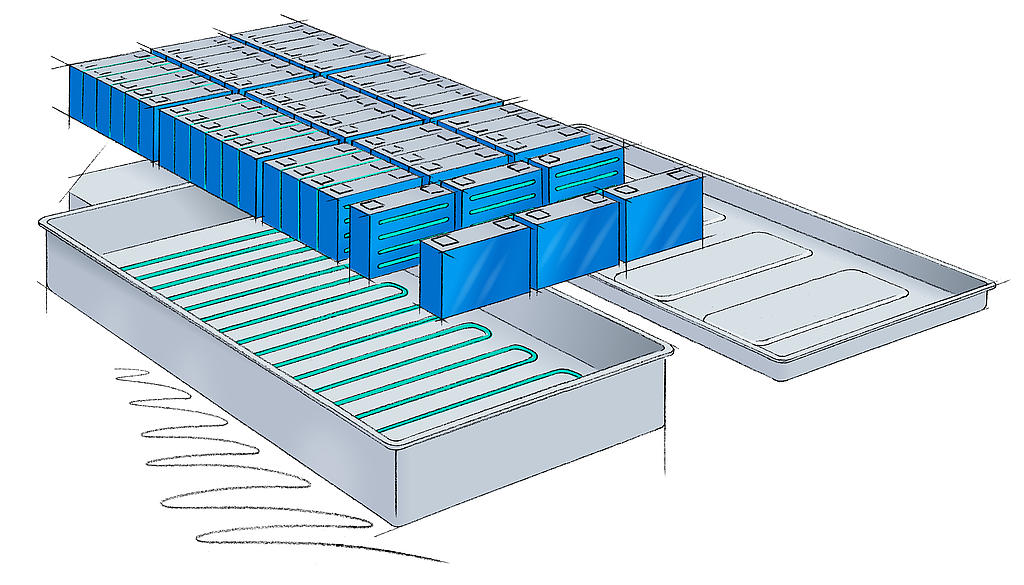
Gap Filler
Gap Filler
The electrochemical reactions in battery cells for e-cars are highly dependent on temperature. That property makes it essential to maintain the battery cells within a healthy temperature window of operation.
In addition, minimizing the temperature differences within the module and pack is crucial to ensuring longevity. Unwanted side reactions in local hot spots within the pack decrease cell capacity and result in continuing loss of overall capacity. Management of the heat flow, for example with the help of ELANTAS gap fillers of silicone or polyurethane chemistry is therefore critical.
Our video will display you more:
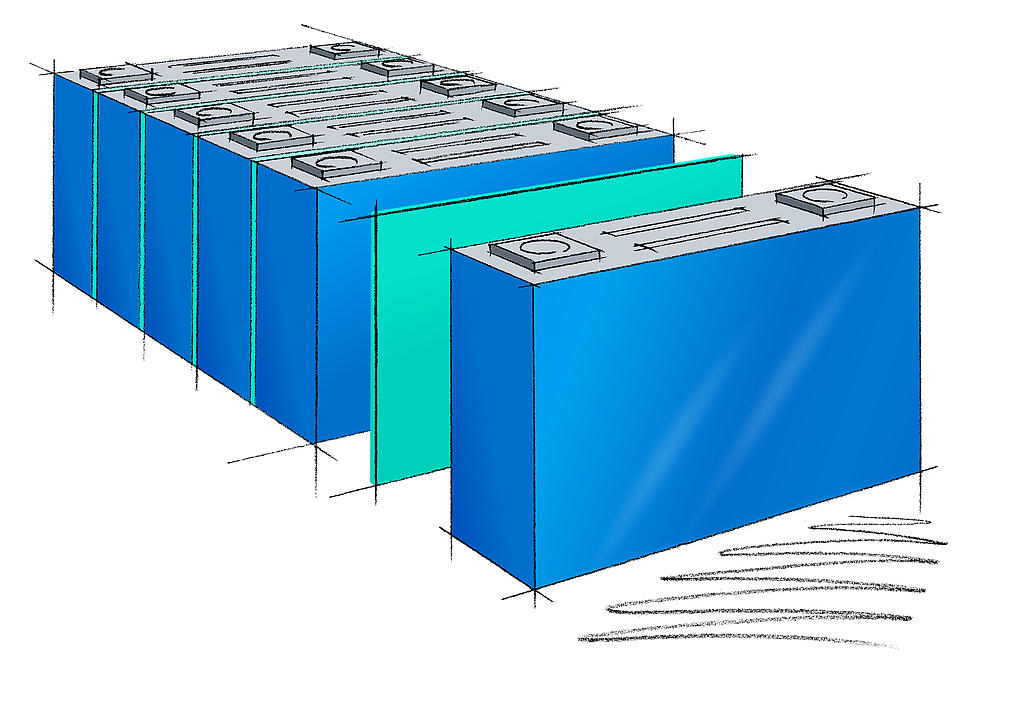
(Thermal) Adhesives
(Thermal) Adhesives
In eMobility applications, the increasing thermal management challenges require heat dissipation across bondlines.
- Adhesives are a proven light-weight, effective bonding solution.
- They must reliably fulfil fixation and provide a path for effective heat transfer.
Examples for thermal adhesives applications are the fixation of cooling elements or heat sinks to the heat source and the cell to cell fixation.
For such applications, ELANTAS epoxy or polyurethane products are highly recommended. They are suitable for most substrates and can be machine applied or dispensed manually, if preferred.
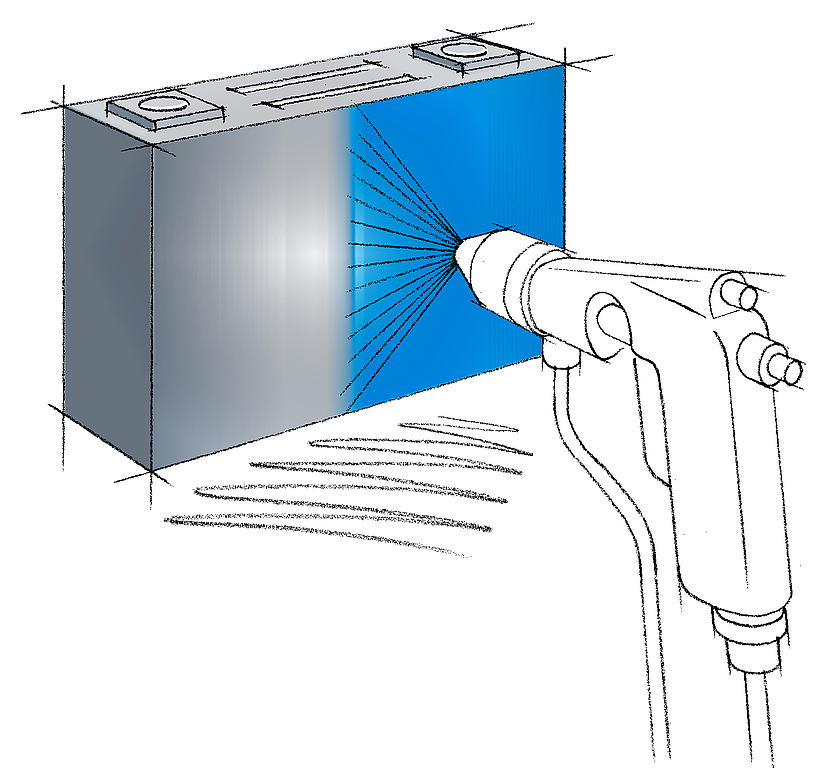
Coatings
Coatings
The complexity of battery packs in electronic vehicles involves several electronic or electric elements that require protection by polymeric coatings. ELANTAS is experienced in various chemistries and application methods, for example:
- The printed cuircuit boards of battery management system at the module or pack level are frequently coated with polymeric resins of various thicknesses to protect them and guarantee longevity.
- Resin coatings are also used on busbars connecting the modules in the pack. Here, the coatings ensure perfect insulation of the conductors to guarantee safe and long-term use under high-voltage conditions in today’s batteries.
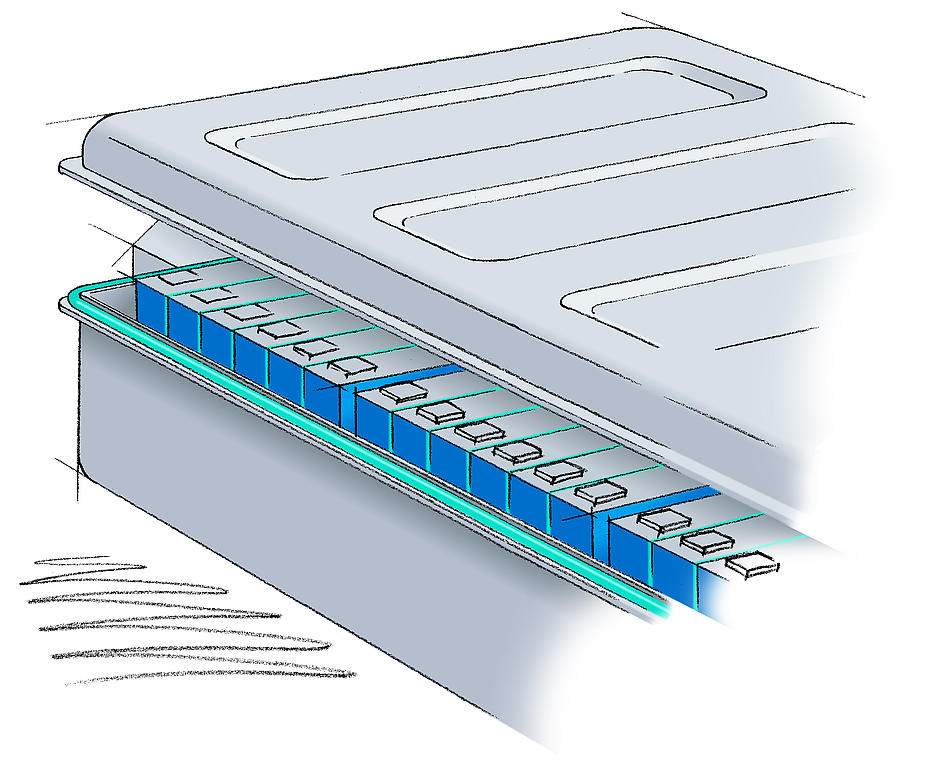
Sealants
Sealants
The anticipated lifetime of a battery pack is about 15 years. Therefore, the housing and all connection points to the pack need to securely sealed.
- ELANTAS sealants protect the valuable interior battery components from water and dirt, which could harm performance.
- They have been shown to withstand stress factors from varying weather conditions and vibrations, as simulated in automotive exposure tests.
Gap Filler
The electrochemical reactions in battery cells for e-cars are highly dependent on temperature. That property makes it essential to maintain the battery cells within a healthy temperature window of operation.
In addition, minimizing the temperature differences within the module and pack is crucial to ensuring longevity. Unwanted side reactions in local hot spots within the pack decrease cell capacity and result in continuing loss of overall capacity. Management of the heat flow, for example with the help of ELANTAS gap fillers of silicone or polyurethane chemistry is therefore critical.
Our video will display you more:
(Thermal) Adhesives
In eMobility applications, the increasing thermal management challenges require heat dissipation across bondlines.
- Adhesives are a proven light-weight, effective bonding solution.
- They must reliably fulfil fixation and provide a path for effective heat transfer.
Examples for thermal adhesives applications are the fixation of cooling elements or heat sinks to the heat source and the cell to cell fixation.
For such applications, ELANTAS epoxy or polyurethane products are highly recommended. They are suitable for most substrates and can be machine applied or dispensed manually, if preferred.
Coatings
The complexity of battery packs in electronic vehicles involves several electronic or electric elements that require protection by polymeric coatings. ELANTAS is experienced in various chemistries and application methods, for example:
- The printed cuircuit boards of battery management system at the module or pack level are frequently coated with polymeric resins of various thicknesses to protect them and guarantee longevity.
- Resin coatings are also used on busbars connecting the modules in the pack. Here, the coatings ensure perfect insulation of the conductors to guarantee safe and long-term use under high-voltage conditions in today’s batteries.
Sealants
The anticipated lifetime of a battery pack is about 15 years. Therefore, the housing and all connection points to the pack need to securely sealed.
- ELANTAS sealants protect the valuable interior battery components from water and dirt, which could harm performance.
- They have been shown to withstand stress factors from varying weather conditions and vibrations, as simulated in automotive exposure tests.
A battery in the field of electromobility serves as the energy store for bikes, scooters, cars, ships or aircrafts. It is always composed of many, sometimes very many, individual cells. The clever parallel and serial connection of cells to modules and packs delivers the desired battery voltage and current.
The cell formats found today are:
- Cylindrical;
- Pouch and
- Prismatic.
Despite the different geometries, the following points are equally important for all cell types during assembly and use:
- Effective thermal management is an important prerequisite for long and consistent performance of a battery. Thermal interface materials ensure effective heat flow.
- At the same time, cell housings shall be insulated electrically. For this reason, a thin layer of an insulative coating can be applied.
- For fixation reasons, either cell-to-cell or cell-to-frame, adhesives can be applied.
Factors for polymer material selection and durability
To meet the above challenges in cell assembly, different polymer materials are used. When selecting them, the local options of product application and the desired properties must be taken into account.
In the final assembly, durability plays an important role:
- End users expect the most stable power output possible during use (driving) and
- fast recharging over the entire service life of the battery.
- The polymer resins must therefore exhibit long-term stability against varying stress factors, such as vibration, temperature and humidity.
ELANTAS offers a wide chemical range of polymeric resins to meet all requirements during application and in the final product.
Gap Fillers
Casting & Potting Resins
Thermal Greases
Thermal Adhesives
A battery module consists of individual cells joined together and is a modular building block for a battery pack. The pack can consist of six, eight or more modules, for example. Adapted to different sized electric cars of some manufacturers, a scaling can be done by more or less modules for each pack
Thermal management is also particularly important in the pack.
The individual modules are mounted on a base plate, which is tempered by coolant.
Good heat transfer between each individual module and the base plate or cooling plate must be ensured. This can be achieved by ELANTAS gap fillers:
- Gap fillers fill the small gap between the module and the plate, thus displacing air as a thermal insulator.
- At the same time, the flexibility of the gap fillers compensates for unevenness in the structures.
- Effective contact between the underside of the module and the cooling plate is important during the period of use. Vibrations and temperature changes during operation must not weaken the adhesion of the gap filler.
TIM (Thermal Interface Material)
Gap Filler
Casting & Potting Resins
Thermal Grease
Thermal Adhesives
Electronic devices continuously analyze a battery’s important operating parameters.
These include temperature monitoring of the modules and also individual cells. Voltage and current flow must be monitored during charging and discharging to ensure that the pack is always in the optimal operating state.
The monitoring and control is done with the help of numerous sensors and one or more battery management systems.
Protection of sensitive battery control electronics
These electronic components are integrated in the battery-pack housing and, like any sensitive electronics, must be protected:
- from vibration damage,
- moisture, and also
- exposure to excessive temperatures.
ELANTAS has many decades of experience in protecting sensitive control electronics. The offer includes different base chemistries and in terms of thickness, ranges from
- Very thin conformal coatings
- thick film coatings
- potting of components.
The curing of the polymer coating can be achieved by
- UV light,
- by heating, and/or moisture curing
The curing reactions follow different mechanisms and can be tuned according to the needs of our customers.
Dielectric Cell Coating / Battery Component Coating
Conformal Coatings
Adhesives
Every assembled cell system requires a housing for protection from external influences such as moisture and corrosive contamination as well as for safe handling and transport.
In electric cars, battery enclosures often consist of an aluminum tray and a cover,sometimes made of another lighter plastic material such SMC or GFC.Other electric vehicles - from electric scooters, robots, boats, aircraft - require housings adapted to the conditions of use and the weight of the battery.
Electrical connections or cooling liquids are fed through the housing wall or the lid of a battery housing. In addition to sealing the cover itself, all feedthroughs must be carefully sealed against ingress of moisture and water with long-term stability.
At the same time, the sealant must withstand the vibration load during operation and the temperature expansion of the base material without damage.
ELANTAS offers:
- sealants on various chemical bases for many material substrates and different requirements,
- Adhesives with sealing effect to help structural fixation and to save weight.
- ELANTAS products are available for application with automatic dispensing equipment as well as for manual application from cartridges.
Sealant Adhesives
The charging infrastructure is key to the success of emobility. Customers expect short and effective charging times that power up the vehicle. With the charging times getting shorter the energy transported over the time gets higher. For this reason, management of heat flow and electrical insulation of the components become more demanding.
Shorter e-car charging times set higher requirements for thermal management and insulation
ELANTAS offers thermal interface materials for the heat flow management as overheating can reduce the lifetime, performance and safety of the equipment. Conformal coatings and casting & potting materials complete the offer for the purpose of electrical insulation of the components of chargers.
The charging infrastructure consists of fast DC charging stations and AC chargers. DC charging stations allow for a fast load of the battery in well under an hour whereas AC chargers require longer time and are often used at home.
To adjust for different vehicles demands converters are needed to convert the voltage to the appropriate level for the vehicle. Control units are use in the charging infrastructure to monitor and steer the processes in the charger and enabling the safe and reliable performance.
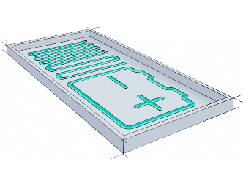
Thermal Interface Materials
Thermal Interface Materials
During the charging cycle of electric vehicles high temperatures are generated which need to be managed as they have a negative effect on the performance and lifetime of the components.
Thermal Interface Materials are the materials of choice as they:
- effectively dissipate heat and
- support heat management in the charging infrastructure.
Highly filled but still low viscous Casting & Potting materials are used for the protection of components like inverter or converter of a charging infrastructure.
They offer the benefits of:
- high thermal conductivity
- self-levelling materials
- void-free filling
- excellent electrical properties
- good chemical resistance
- good thermal properties
Gap Filler which are higher viscous and thixotropic by design are used in areas where material flow is not needed. Benefits gained by Gap Fillers are:
- high thermal conductivity,
- application in bead form
- easy to dispense,
- excellent electrical properties,
- good chemical resistance, and
- good thermal properties.
The materials are easily applied with standard mass production equipment. The ELANTAS ELAN-tim Portfolio offers different chemistries to find the right fit for the application.
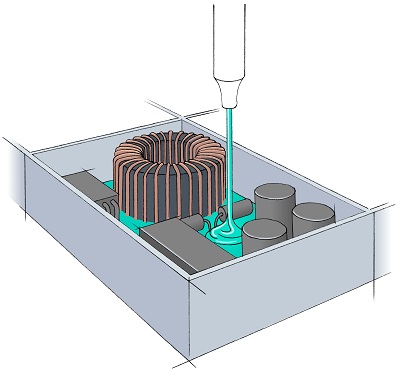
Casting & Potting Materials
Casting & Potting Materials
Casting and Potting materials with lower thermal conductivity are used for applications where thermal management is not paramount, e.g. ...
- The materials have a low viscosity and can be easily dosed by standard manufacturing equipment.
- They protect components such as converters and inverters from moisture, chemicals, and mechanical shock and vibration, while offering electrical insulation.
ELANTAS has a broad portfolio of different chemistries that can be selected depending on application requirements. All materials offer:
- good flow behavior for void-free filling of components
- self-levelling properties
- excellent electrical properties
- good chemical resistance
- good thermal properties
All materials can be applied with standard mass-production equipment.
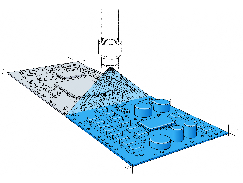
Conformal Coatings
Conformal Coatings
Conformal Coatings are used to protect printed circuit boards (PCB) with film coating. They ensure the safe and reliable performance of electronics wherever a controller is needed in the charging infrastructure.
- They protect the board against external factors like humidity, chemicals and dust.
- In addition they have excellent electrical properties and help to insulate the PCBs.
- The materials can be applied with standard mass-production equipment.
Depending on application requirements, different chemistries and curing mechanisms are available from ELANTAS.
Thermal Interface Materials
During the charging cycle of electric vehicles high temperatures are generated which need to be managed as they have a negative effect on the performance and lifetime of the components.
Thermal Interface Materials are the materials of choice as they:
- effectively dissipate heat and
- support heat management in the charging infrastructure.
Highly filled but still low viscous Casting & Potting materials are used for the protection of components like inverter or converter of a charging infrastructure.
They offer the benefits of:
- high thermal conductivity
- self-levelling materials
- void-free filling
- excellent electrical properties
- good chemical resistance
- good thermal properties
Gap Filler which are higher viscous and thixotropic by design are used in areas where material flow is not needed. Benefits gained by Gap Fillers are:
- high thermal conductivity,
- application in bead form
- easy to dispense,
- excellent electrical properties,
- good chemical resistance, and
- good thermal properties.
The materials are easily applied with standard mass production equipment. The ELANTAS ELAN-tim Portfolio offers different chemistries to find the right fit for the application.
Casting & Potting Materials
Casting and Potting materials with lower thermal conductivity are used for applications where thermal management is not paramount, e.g. ...
- The materials have a low viscosity and can be easily dosed by standard manufacturing equipment.
- They protect components such as converters and inverters from moisture, chemicals, and mechanical shock and vibration, while offering electrical insulation.
ELANTAS has a broad portfolio of different chemistries that can be selected depending on application requirements. All materials offer:
- good flow behavior for void-free filling of components
- self-levelling properties
- excellent electrical properties
- good chemical resistance
- good thermal properties
All materials can be applied with standard mass-production equipment.
Conformal Coatings
Conformal Coatings are used to protect printed circuit boards (PCB) with film coating. They ensure the safe and reliable performance of electronics wherever a controller is needed in the charging infrastructure.
- They protect the board against external factors like humidity, chemicals and dust.
- In addition they have excellent electrical properties and help to insulate the PCBs.
- The materials can be applied with standard mass-production equipment.
Depending on application requirements, different chemistries and curing mechanisms are available from ELANTAS.
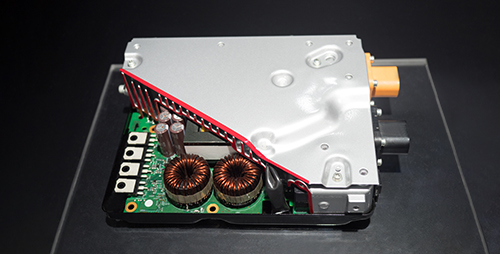
DC Charging stations offer the fastest way to charge a vehicle. They support customer expectations of a short charging cycle that enables them to drive longer distances with short stops for charging. For this the AC power of the grid needs to be inverted to DC current required for the short charging process.During the charging cycle extensive heat is generated and heat management of the components becomes crucial for enabling safe and reliable performance.
The ELAN-tim® thermal interface materials can help with the heat management. The Gap Filler and Casting & Potting materials show high functionality due to their high thermal conductivity and can be used to encapsulate the components.
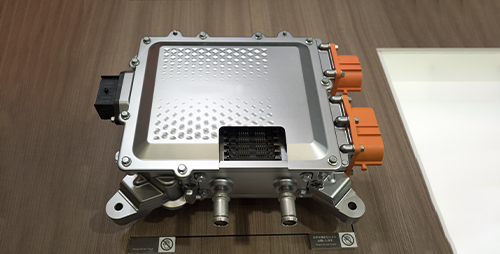
The fixed DC voltage that is provided by the AC/DC converter is transformed by the DC/DC converter in the charging station to the right voltage level needed for charging a specific vehicle. To ensure fast charging the energy density is high and likewise the generation of heat. Heat management becomes paramount for the safe and reliable performance.
Using Casting & Potting materials like the ELAN-tim® products for insulation purposes supports the heat management in the converters. The products have high thermal conductivity and dissipate heat away fast from the sensitive components.
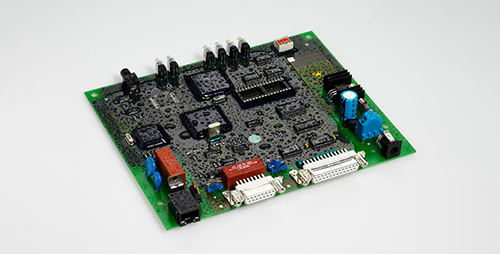
The charging infrastructure can’t function without several control units. They make sure that the equipment is working smoothly and reliable. The core of those units are printed circuit boards which need to be insulated and protected against environmental effect (e.g. humidity).
Conformal Coatings are applied to the circuit boards to protect them and ensure reliable performance. Under the brand names Bectron, CONAP and Conathane ELANTAS offers materials that are widely used in the automotive industry for decades.
ELANTAS provides thermal interface materials that support the heat flow management to ensure safe and reliable long lifetime of the power electronics’ components. Conformal coatings and casting & potting materials that electrically insulate all components.
Power electronics are the key parts in the powertrain of an electric vehicle. They help to manage the energy flow and keep the car going.
- Inverters convert direct current (DC) from the battery to provide alternating current (AC) for the motor and other components. To adjust for the different voltage levels needed in the vehicle converters like DC/DC are installed to convert the power from one voltage to another.
- Onboard chargers make sure that AC power can be used to charge the vehicle in addition to DC current from charging stations and optimize the charging process.
- In addition, different controller units are installed.
For all Power Electronics the electrical insulation and heat management are key to make sure that all the processes in the powertrain are running smoothly and enabling the safe and reliable performance of the electric car.
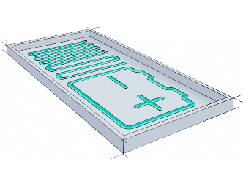
Thermal Interface Materials
Thermal Interface Materials
Thermal interface materials are highly filled materials that are optimized to dissipate heat and help the thermal management of Power Electronics.
ELANTAS offers Casting & Potting materials based on different chemistries with excellent properties such as:
- high thermal conductivity,
- low viscosity for fast self levelling and void-free filling of the component
- excellent electrical properties
- thermal stability based on chemistry
- chemical resistance based on chemistry
They can be used within electric-vehicle applications for
- converters,
- inverters,
- on-board chargers and
- other components of the powertrain
In addition, gap fillers are available for areas where material needs to be applied in beads. They have the benefit of:
- high thermal conductivity ,
- thixotropic flow behavior – no self levelling,
- easy to dispense,
- excellent electrical properties,
- thermal stability based on chemistry chosen,
- chemical resistance based on chemistry chosen.
Different chemistries and thermal conductivities are part of the ELANTAS portfolio which is branded under the tradename ELAN-tim. All materials can be applied with standard dispensing equipment commonly used in production.
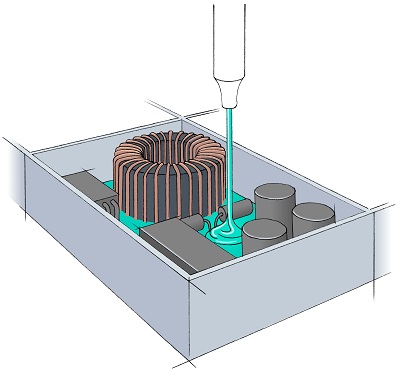
Casting & Potting Materials
Casting & Potting Materials
Next to Thermal Interface Materials Casting and Potting materials are used for the protection of the power electronics:
- to protect High and Low voltage converter or DC / DC converter from environmental impacts like moisture and chemicals and also
- to provide protection against mechanical shock or vibration.
- in addition they have excellent insulating properties.
The materials are easy to apply using standard production equipment due to their low viscosity. Different chemistries are available, depending on the application need. The materials offer:
- self-levelling due to flow properties
- void-free filling
- excellent electrical properties
- thermal stability based on chemistry chosen
- chemical resistance based on chemistry chosen
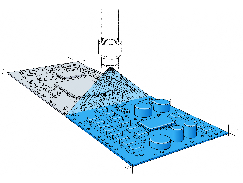
Conformal Coatings
Conformal Coatings
Conformal coatings are state-of-the-art for protection of printed circuit boards (PCB) and are applied in a thin film.
- They protect the PCB against environmental impacts like dust, moisture and chemicals.
- They are electrical insulators and ensure the reliable performance of controllers in power electronics or other electronic parts in the vehicle.
- The conformal coatings can be applied with standard equipment used for mass production.
ELANTAS offers different chemistries and curing mechanisms to find the best solution for the application requirements. All materials can be applied with standard mass-production equipment.
Thermal Interface Materials
Thermal interface materials are highly filled materials that are optimized to dissipate heat and help the thermal management of Power Electronics.
ELANTAS offers Casting & Potting materials based on different chemistries with excellent properties such as:
- high thermal conductivity,
- low viscosity for fast self levelling and void-free filling of the component
- excellent electrical properties
- thermal stability based on chemistry
- chemical resistance based on chemistry
They can be used within electric-vehicle applications for
- converters,
- inverters,
- on-board chargers and
- other components of the powertrain
In addition, gap fillers are available for areas where material needs to be applied in beads. They have the benefit of:
- high thermal conductivity ,
- thixotropic flow behavior – no self levelling,
- easy to dispense,
- excellent electrical properties,
- thermal stability based on chemistry chosen,
- chemical resistance based on chemistry chosen.
Different chemistries and thermal conductivities are part of the ELANTAS portfolio which is branded under the tradename ELAN-tim. All materials can be applied with standard dispensing equipment commonly used in production.
Casting & Potting Materials
Next to Thermal Interface Materials Casting and Potting materials are used for the protection of the power electronics:
- to protect High and Low voltage converter or DC / DC converter from environmental impacts like moisture and chemicals and also
- to provide protection against mechanical shock or vibration.
- in addition they have excellent insulating properties.
The materials are easy to apply using standard production equipment due to their low viscosity. Different chemistries are available, depending on the application need. The materials offer:
- self-levelling due to flow properties
- void-free filling
- excellent electrical properties
- thermal stability based on chemistry chosen
- chemical resistance based on chemistry chosen
Conformal Coatings
Conformal coatings are state-of-the-art for protection of printed circuit boards (PCB) and are applied in a thin film.
- They protect the PCB against environmental impacts like dust, moisture and chemicals.
- They are electrical insulators and ensure the reliable performance of controllers in power electronics or other electronic parts in the vehicle.
- The conformal coatings can be applied with standard equipment used for mass production.
ELANTAS offers different chemistries and curing mechanisms to find the best solution for the application requirements. All materials can be applied with standard mass-production equipment.
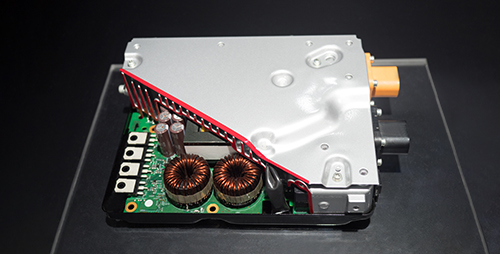
Every powertrain contains an inverter that converts the DC current from the battery into the AC current needed to power the motor. The inverter is essential to the performance of the motor and influences driving behavior. During the power conversion process, heat is generated, which can have a negative effect on the performance and longevity of the inverter.
With the ELAN-tim product range, ELANTAS offers thermal conductive casting and potting materials that support the active heat management in the inverter.
Another key part of the inverter is a printed circuit board as a control unit, which steers the processes in the inverter.
Here ELANTAS offers a broad range of conformal coatings to protect the circuit boards against environmental impacts and insulate them.
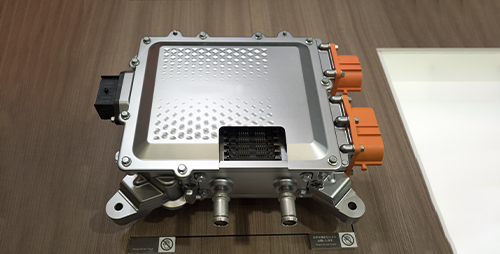
The HV battery is powering the motor and the other systems in the vehicle. Not every system needs a high voltage: certain components, like the entertainment or safety systems, run on lower voltages.
For this purpose, DC/DC converters are present, which changes the voltage accordingly.
During the conversion process, heat is generated that needs to be transferred away from the sensitive components as overheating can lead to failure and reduced lifetime.
With the ELAN-tim® product group of thermal conductive materials, ELANTAS offers thixotropic gap filler and free-flowing casting and potting materials that help to optimize the heat management in the powertrain. The material can be applied with standard mass-production equipment.
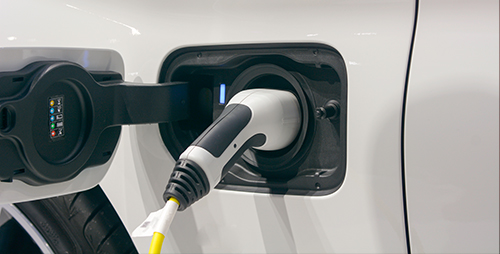
On Board Chargers are present in most EV and HEV and allow charging of the vehicle with AC current either at home or at charging stations. The charger contains power inverter and converter so that the input AC current can be transformed to the voltage and current level the battery needs. During the charging process heat is generated in the components which need to be dissipated as overheating reduces the lifetime and reliability of the components.
Thermal Interface Materials like ELAN-tim® Casting & Potting materials can be used to insulate the components and to help dissipate the heat away from them. The printed circuit board control unit that is in the charger also needs to be insulated with a Conformal Coating to ensure safe performance.
All material can be applied with mass production equipment standard to the industry.
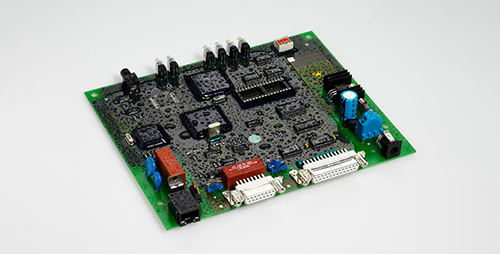
Control Units are present in the whole power train of the vehicles. The heart of those units is a printed circuit board which is controlling all processes and ensures that the vehicle is working safely and reliably. Conformal Coatings are a common and widely used products in the industry to protect the printed circuit boards against dust, humidity, moisture and chemicals. They insulate the boards and ensure longevity.
ELANTAS offers differs chemistries that are suitable for coating the control units. The Bectron, CONAP and Conathane materials are used in the automotive sector since decades and are proven solutions. All products can be applied with standard industrial mass-production equipment.